How to Build a Wine Cellar
Step 1: Identify the Purpose of Your Wine Cellar
- Will your wine cellar simply be for functional long term storage or more of a showcase for your wine?
- How many bottles and what types of wine will you be storing?
- Knowing the answer to these questions will help you determine the wine cellar size that will meet your needs.
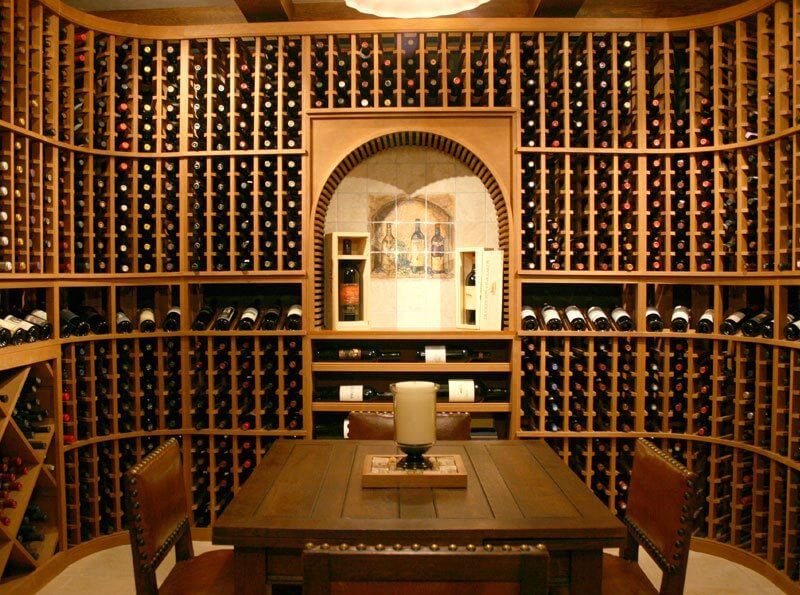
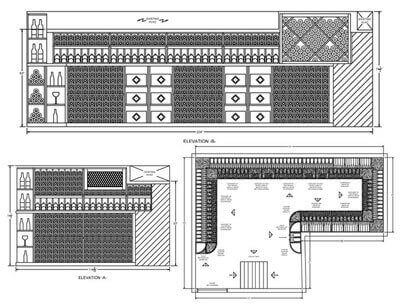
Step 2: Determine Your Wine Cellar Size
The size of your wine cellar will depend on how many bottles you wish to store and how much space you can devote to it. Our wine cellar construction charts are a great tool to help you understand the space you will need, the materials to use and the average construction costs.
Step 3: Choose Your Wine Cellar Location
The location chosen determines many other factors affecting the cost of building and maintaining the cellar. The ideal temperature and humidity for a wine cellar is in the 55°F and 60% relative humidity range. If you select a cooler, more humid location, the cooling system will not need to work as hard so a smaller cooling system may be adequate. This may translate to lower energy costs. Conversely, a warmer location means the cooling system will run more frequently and a larger system may be required. Construction cost may also increase as additional insulation may be required.
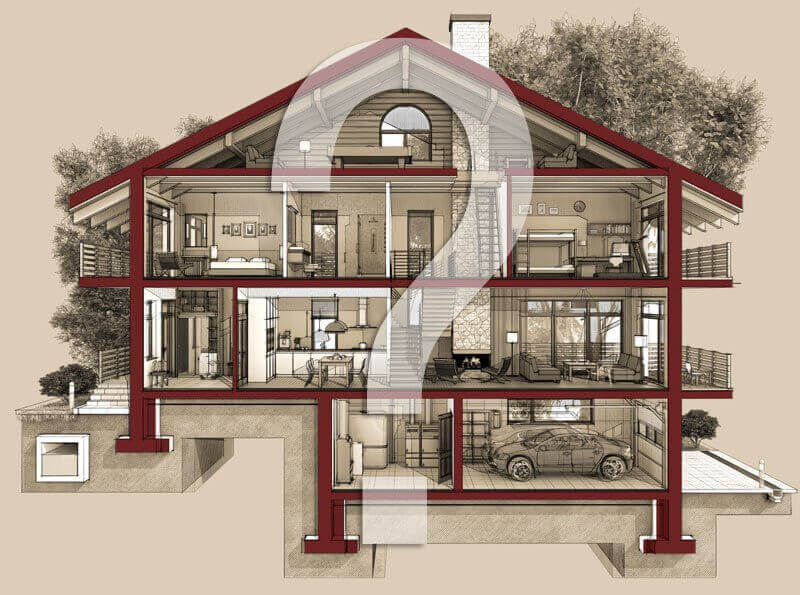
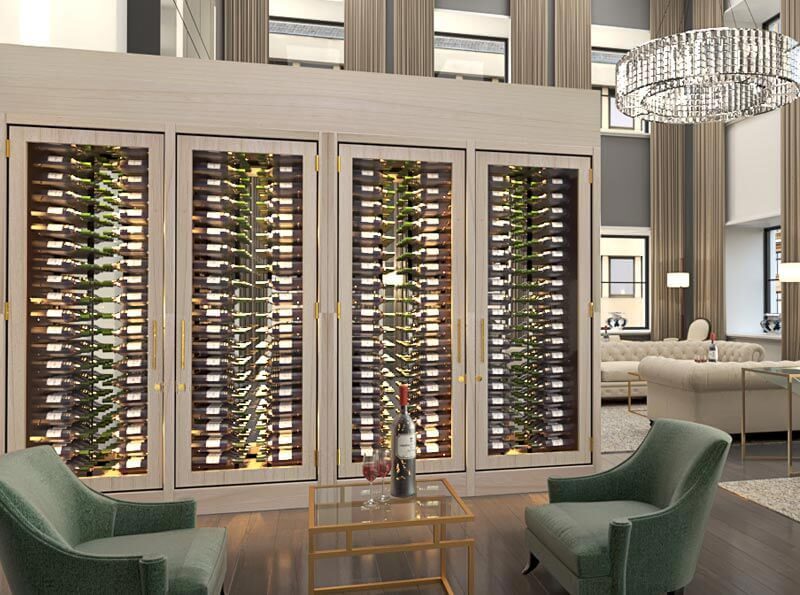
Step 4: Wine Cellar Temperature
What Cooling System Works?
Your wine cellar should be placed in the coolest, most humid area in your home. The closer the wine room is to an ideal wine cellar temperature of 55° F and 60-65% Relative Humidity, the more efficient the cooling system will be. Any warmer and your wine will age faster; any cooler and your wine will age slower.
The location and size of the wine cellar will determine what cooling system is going to work best for the space. Some wine cellar cooling systems have strict requirements for installation. For example, a through the wall cooling system cannot vent directly into living space. So if your wine cellar is in the center of your living space, this system would not be a fit for you. A ducted or ductless system would be a better choice. The selection of and planning for a wine cellar cooling system should done prior to the wine cellar framing stage.
Step 5: Do I Need a Vapor Barrier?
The application of vapor barrier is critical to the maintaining the correct environment and preventing moisture from forming inside your wine cellar walls. The method used will depend on what insulation material is being used.
- If traditional batting or rigid foam is to be installed, then you must wrap the walls and ceiling with a 6mil poly vapor barrier so the room is completely sealed.
- If the cellar is not in a basement, you will need to install the vapor barrier and insulate the floor as well. Be sure to tape all of the joints of poly with moisture resistant tape and be sure to seal all outlets and lighting fixtures that penetrate the barrier.
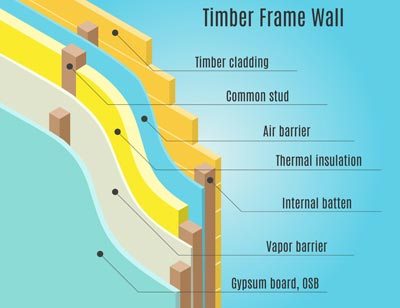
Insulation Considerations
- Insulation isolates your wine cellar from exterior elements and helps to maintain a cool, moist environment for your wine. It will keep your passive cellar from becoming too warm and will help to conserve energy for a wine room that is actively cooled by a system.
- Non-cement floors with living or crawl spaces below must be insulated with rigid foam, spray-in insulations-preferably closed cell, or traditional fiberglass batting. Vapor barrier must also be applied on these surfaces as well.
- Walls must be insulated with a minimum value of R-19 and ceilings must be insulated with a value of R-30. R-value indicates the ability of the insulation to restrict heat flow — a higher R-value indicates better insulation.
- When applying traditional fiberglass batting, make sure to orient the paper or foil barrier toward the warm side of the wine cellar wall. Seal all joints with a foil-backed tape.
- When insulating your wine cellar, more is always better. Standard fiberglass rolls or batting provide an R-value of approximately 3 per inch.
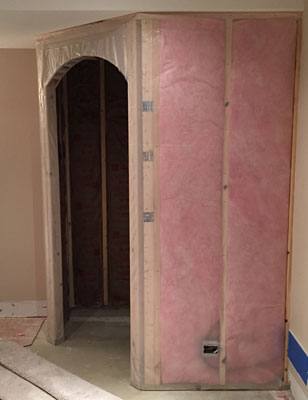
Construction Material Thicknesses and R-Values
Wall Frame Thickness | Insulation Thickness | R-Value Fiberglass Batting | R-Value Rigid Foam |
---|---|---|---|
4" | 3.5" | R-11 | R-25 |
6" | 5.5" | R-19 | R-39 |
10" | 9" | R-30 | R-65 |
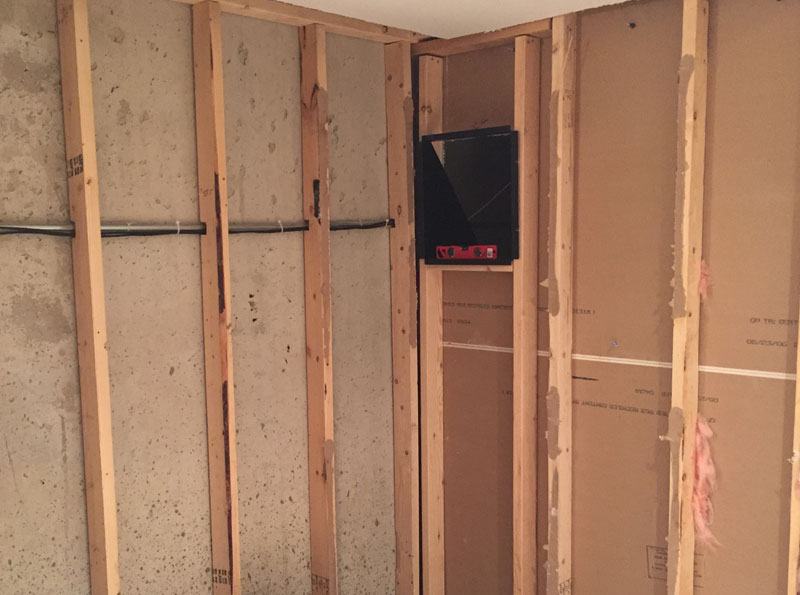
Step 6: What Should I Frame and Insulate in My Wine Cellar?
If you are using spray in closed cell foam insulation, this acts as a vapor barrier as well as an insulator so the 6 mil poly step in the vapor barrier process is not necessary.
Wine Cellar Construction Reference Chart
Construction Step | Recommended Specifications |
---|---|
Wall Framing | 2" x 6" @ 16" on center |
Ceiling Framing | 2" x 8" @ 16" on center |
Vapor Barrier | 6 mil polyethylene on warm side of walls and ceilings. Check your local building codes |
Wall Insulation | R-19 minimum |
Ceiling Insulation | R-30 minimum |
Sheathing | DensArmor Plus® Interior Drywall is our recommended sheathing. You can also use 1/2" moisture resistant green board with mildew resistant paint or a tongue and groove wood paneling like mahogany |
Flooring | Moisture resistant material such as brick, tile, stone or hardwoods |
Electrical Considerations
- Upon completion of the wall framing, run all electrical wiring for lighting, outlets and your wine room cooling system.
- Cooling systems normally require a dedicated circuit, so check the manufacturer’s instructions and voltage requirements.
- Light switches with dimmers, if desired should be placed near the wine cellar door and should control all the lighting in the wine cellar. Switches with timers or motion detectors are a nice feature that can turn the lights off for you when your hands are full. This is the time to start thinking about what kind of lighting fixtures you would like and to have the wires run for them. Consider sconces, chandeliers, recessed lighting, can lighting and track lighting.
Step 7: Determine Your Materials
After the cellar is framed, sealed, insulated and all electrical and plumbing has been roughed in, you will chose your wall, ceiling and flooring materials.
- A moisture resistant drywall/plywood material is fine for walls and ceiling. We recommend DensArmor Plus® Interior Drywall. You can also use 1/2″ moisture-resistant gypsum wall board or green board is the most common and cost effective wall material. This wall board must be painted with a moisture resistant paint.
- Rot resistant hardwoods are an attractive alternative and while more expensive to purchase and install, provide a superior appearance and require no long-term maintenance. Wood paneling works well for this also.
- For flooring, you want to choose a flooring material that will hold up in the cool humid wine cellar environment. Tile, stone and brick work well as does wine barrel flooring that is made from recycled wine barrel staves.
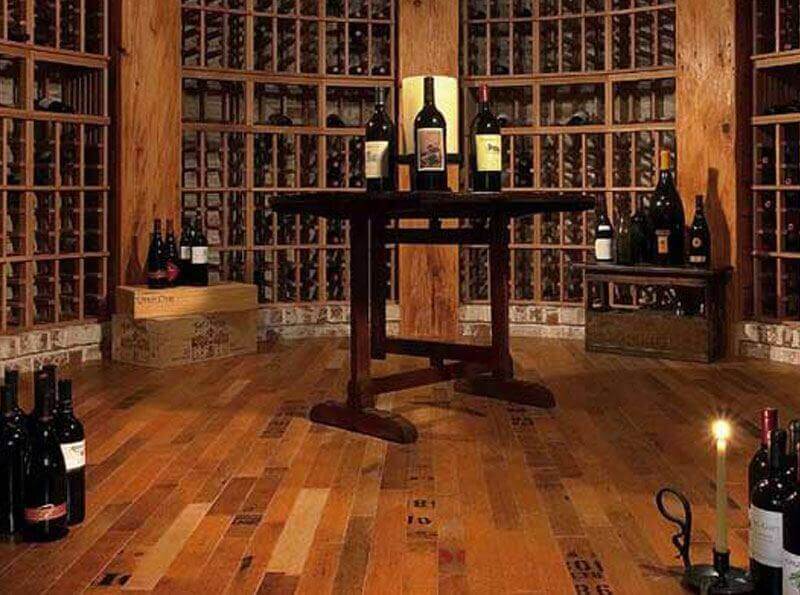
Step 8: Choose Your Entry Door
It is preferable to have your wine cellar door swing into the wine cellar, but make sure that its swing path does not interfere with your wine racks. The positive pressure in a conditioned wine room will push the in-swinging door against the jamb and weather stripping, creating a superior seal. Before ordering your door you must determine its swing; in or out, and left or right. Make sure to provide this information to whomever you choose to manufacture your wine cellar door.
When choosing a door with a glass panel, make sure that the panel is dual paned, insulated glass. The higher the R-value, the better. All Vigilant glass doors include Argon filled, insulated, tempered glass panels that offer twice the R-value than standard insulated glass. If adding windows or sidelights to your wine room be sure they meet all of the same performance specifications as your wine cellar door.
Step 9: How Do I Begin The Wine Storage Design Process And Select The Proper Wine Rack Components?
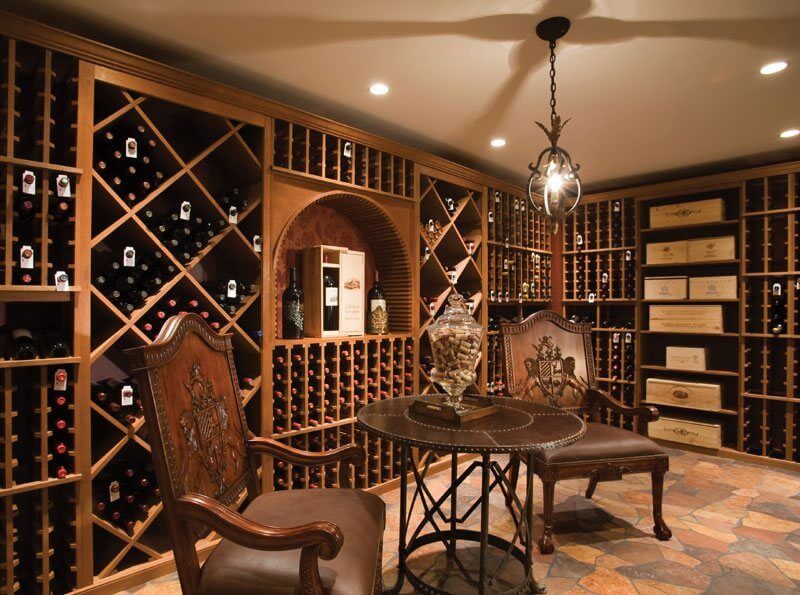
Our Custom Wine Racking
Our DIY Wine Racking Kits
Our do-it-yourself or kit wine racks consist of an extensive line of pre-built wine storage racks and wine cabinets that can be combined to create a complete wine cellar storage solution. At 77.5″ or 92.5″ high and 13.5″ deep, they are of the same quality as our custom wine racks, but have these distinct advantages.
- They are available for quick shipment
- They can be combined to create a custom looking wine cellar
- Many can be modified to fit any wine room configuration
- They are less expensive than custom wine racking
Wine Rack Costs
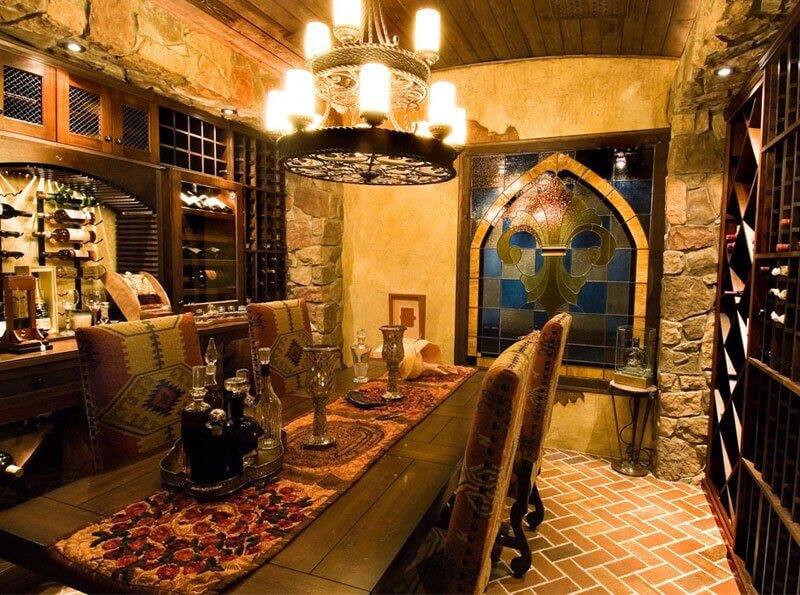
Step 10: Decorating Your Wine Cellar
Whatever your style, whether it’s traditional, rustic, modern or contemporary, decorating with elements you love can help you achieve your unique custom looking wine cellar. Choosing the details of your wine cellar is an exciting way to create a room that becomes a showcase of your style and taste. Wine cellars are so much more than just storing your wine bottles — your wine cellar decorating should reflect the beauty and uniqueness of you and your wine collection.
Designing a Wine Cellar
Following these basic steps when designing a wine cellar with us will ensure that your project goes smoothly and that your cellar turns out exactly the way you desire.
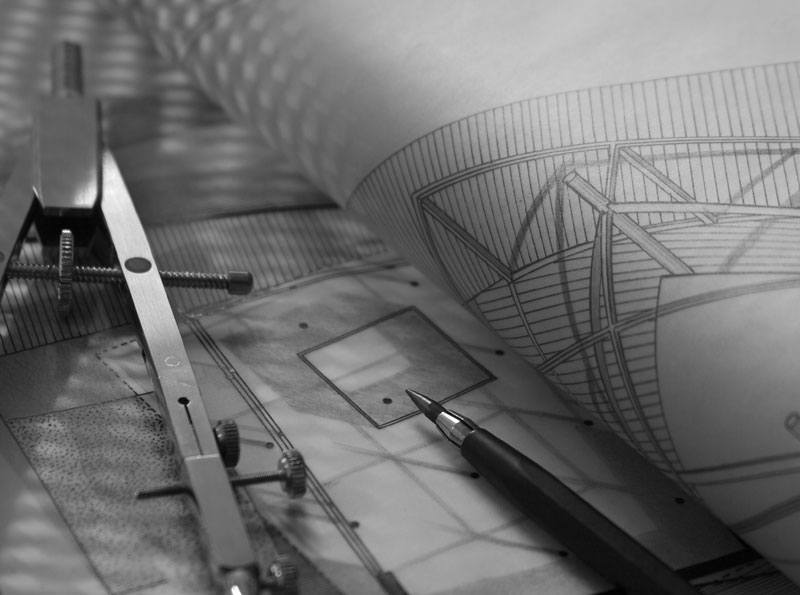
1. Preparation
- Determine exactly where the wine cellar will be located.
- Establish the planned finished dimensions of your wine room, including ceiling height and location of your wine cooling system and wine cellar door.
- Estimate the number of wine bottles that you would like your wine cellar to hold. View our wine cellar construction charts to start estimating bottle capacity and overall costs.
- Decide if you will be designing a Vigilant kit wine cellar or a custom wine cellar.
- Choose the racking elements and features you want in your wine cellar.
2. Initial Design Request
- Provide us with room dimensions, architectural drawings, or a hand-drawn floor plan of your wine cellar space with as many dimensional and storage details as possible.
- Complete our Design Request Form and submit it to our consultants with your floor plan.
- A design consultant will contact you to discuss the details of your project within 48 business hours.
3. Design and Proposal
Based on the information received from your submittal and consultation, our design team will create a complimentary design and proposal for your review. Larger more complex projects may require a design deposit to initiate the proposal and design process.
4. Final Drawing
After reviewing your drawing with your Vigilant consultant, it will be time to make some decisions on your project. Whether you are satisfied with the design and proposal or would like to make changes. We ask for a project deposit at this juncture to continue working on the project and any additional design work is billed out at an hourly rate. Please contact your Vigilant sales consultant for more information.
If you decide you want to move forward with us on your wine cellar project we collect your deposit, and provide you with a final drawing and proposal.
5. Ordering
Once you are fully satisfied that the design and proposal perfectly fit your needs and you are ready to proceed:
- The drawings and proposal are signed.
- A full project deposit is paid to put the job into production. A 50% Kit or 20% Custom Design Deposit (100% of which is credited towards your order.
- We will send you a projected ship date for your order.
Ask your Design consultant about production lead times for our products.